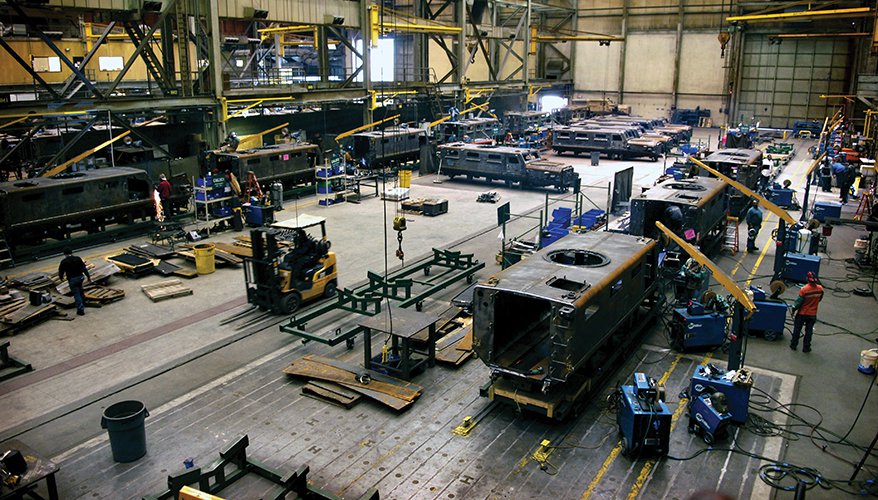
Occasionally things go wrong. In these situations, we must determine the cause. When this happens, we use the process of asking questions called the Five Whys to determine the cause of a particular problem.
The 5 Whys can help teams solve problems by helping them communicate. It fosters curiosity and helps teams understand one another's perspectives so they can work together to find solutions. The system also acts as a backup interrogation tool for team members who are unsure why an issue occurred, or what they can do to resolve it.
What is the Five Whys Method?
The five whys is a quick and effective way to identify the root cause of any problem. The five whys technique is effective in resolving moderate to simple issues. However, it can be used for more complex problems.
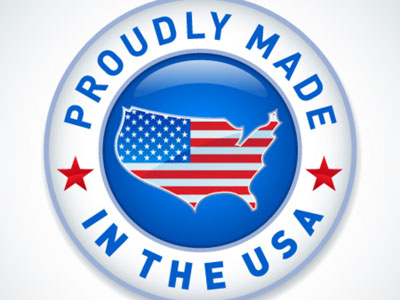
In some cases, the nature of a problem may require more than five possible reasons to be used during the investigation. It is important to remember this when the root cause of a problem can be multiple.
The 5 Whys Method: How to Use it
It is important to put together a team that has experience in the area. The team can consist of individuals from different departments and sectors. It will enable them to offer a diverse range of perspectives and ideas that may help better pinpoint the root cause of any problem.
Once the team is assembled, they should discuss the problem at hand and begin asking each of the five whys questions. The team will be able to identify the cause of the problem and decide if there are any immediate solutions or long-term countermeasures that can prevent the problem from happening again.
They should then carefully examine each question to see if the answer is reasonable. This is a crucial step, as it gives the analyst confidence that he or she is on their way to a successful conclusion.
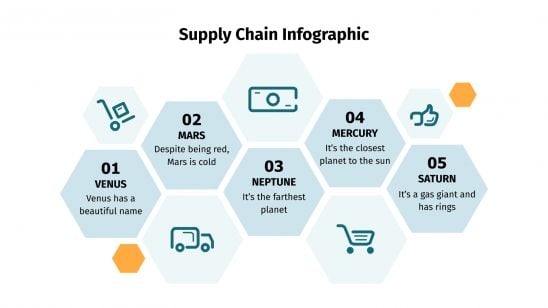
It is important to continue asking these five questions until the root causes of the issue are identified. This will allow them to come up a list with countermeasures and prevent it from recurring in the future. They should then assign each of these corrective actions to the member of the team that can be held responsible for them.
The five whys are a great way to pinpoint the root causes for any issue within your organisation. It is most effective when used with other tools to understand root causes, like FMEA analysis or cause-and effect analysis.
FAQ
What is production planning?
Production Planning refers to the development of a plan for every aspect of production. It is important to have everything ready and planned before you start shooting. You should also have information to ensure the best possible results on set. This includes information on shooting times, locations, cast lists and crew details.
The first step in filming is to define what you want. You may have already decided where you would like to shoot, or maybe there are specific locations or sets that you want to use. Once you've identified the locations and scenes you want to use, you can begin to plan what elements you need for each scene. Perhaps you have decided that you need to buy a car but aren't sure which model. If this is the case, you might start searching online for car models and then narrow your options by selecting from different makes.
After you have selected the car you want, you can begin to think about additional features. What about additional seating? Maybe you need someone to move around in the back. Maybe you'd like to change the interior from black to a white color. These questions can help you decide the right look for your car. The type of shots that you are looking for is another thing to consider. Will you be filming close-ups or wide angles? Maybe you want the engine or the steering wheels to be shown. All of these things will help you identify the exact style of car you want to film.
Once you've determined the above, it is time to start creating a calendar. A schedule will tell you when you need to start shooting and when you need to finish. You will need to know when you have to be there, what time you have to leave and when your return home. Everyone will know what they need and when. Book extra staff ahead of time if you need them. It is not worth hiring someone who won’t show up because you didn’t tell him.
It is important to calculate the amount of filming days when you are creating your schedule. Some projects take only a few days while others can last several weeks. While creating your schedule, it is important to remember whether you will require more than one shot per day. Multiplying takes in the same area will result both in increased costs and a longer time. It's better to be safe than sorry and shoot less takes if you're not certain whether you need more takes.
Budgeting is another crucial aspect of production plan. It is important to set a realistic budget so you can work within your budget. If you have to reduce your budget due to unexpected circumstances, you can always lower it later. But, don't underestimate how much money you'll spend. If you underestimate how much something costs, you'll have less money to pay for other items.
Production planning can be a complex process. However, once you know how everything works together it will become easier to plan future projects.
How can I find out more about manufacturing?
Practical experience is the best way of learning about manufacturing. But if that is not possible you can always read books and watch educational videos.
How can manufacturing reduce production bottlenecks?
Production bottlenecks can be avoided by ensuring that processes are running smoothly during the entire production process, starting with the receipt of an order and ending when the product ships.
This includes planning to meet capacity requirements and quality control.
This can be done by using continuous improvement techniques, such as Six Sigma.
Six Sigma is a management system used to improve quality and reduce waste in every aspect of your organization.
It focuses on eliminating variation and creating consistency in your work.
Statistics
- According to the United Nations Industrial Development Organization (UNIDO), China is the top manufacturer worldwide by 2019 output, producing 28.7% of the total global manufacturing output, followed by the United States, Japan, Germany, and India.[52][53] (en.wikipedia.org)
- Job #1 is delivering the ordered product according to specifications: color, size, brand, and quantity. (netsuite.com)
- In 2021, an estimated 12.1 million Americans work in the manufacturing sector.6 (investopedia.com)
- [54][55] These are the top 50 countries by the total value of manufacturing output in US dollars for its noted year according to World Bank.[56] (en.wikipedia.org)
- Many factories witnessed a 30% increase in output due to the shift to electric motors. (en.wikipedia.org)
External Links
How To
Six Sigma: How to Use it in Manufacturing
Six Sigma refers to "the application and control of statistical processes (SPC) techniques in order to achieve continuous improvement." It was developed by Motorola's Quality Improvement Department at their plant in Tokyo, Japan, in 1986. Six Sigma is a method to improve quality through standardization and elimination of defects. Many companies have adopted Six Sigma in recent years because they believe that there are no perfect products and services. Six Sigma seeks to reduce variation between the mean production value. You can calculate the percentage of deviation from the norm by taking a sample of your product and comparing it to the average. If it is too large, it means that there are problems.
Understanding the nature of variability in your business is the first step to Six Sigma. Once you have this understanding, you will need to identify sources and causes of variation. These variations can also be classified as random or systematic. Random variations occur when people make mistakes; systematic ones are caused by factors outside the process itself. If you make widgets and some of them end up on the assembly line, then those are considered random variations. But if you notice that every widget you make falls apart at the exact same place each time, this would indicate that there is a problem.
Once you've identified the problem areas you need to find solutions. That solution might involve changing the way you do things or redesigning the process altogether. After implementing the new changes, you should test them again to see if they worked. If they don't work, you will need to go back to the drawing boards and create a new plan.