
The United States ranks third among the largest manufacturers in the world. In Q1 2018, its manufacturing output topped $2.00 trillion. This is nearly twice what it was prior to the Great Recession. Despite the strong domestic economy, the United States' manufacturing industry continues to take a sloppy approach to solving its current problems. This is either due to a lack in investment or a shortage of skilled labor. We must be more aggressive in confronting the challenges that face our industry.
Since 2000, jobs have dropped by 5 million
Since 2000, the US has lost five millions manufacturing jobs. Some believe the increase in trade with China is to blame, but this explains only about a fourth of the decline in manufacturing jobs. Manufacturing jobs were also lost in countries that couldn't compete with Chinese imports. There are many reasons why manufacturing jobs have declined. These are just a few of the many reasons.
Over the past two decades, almost a third have been lost in US manufacturing. It was 17 million people in 1965. In 2010, it was only 12 million. Although the decline of manufacturing jobs is not due solely to trade, it is the result structural problems such as a fall in capital investment and output. These are not sustainable. While productivity gains were a key factor in the decline, they were not sufficient to offset the loss manufacturing jobs. Automation is the problem, not productivity increases.
Strong demand exists for manufactured goods
The demand for manufactured goods in the United States remains strong, despite the fact the percentage of consumers spending on them has declined over the last few decades. In 1945 personal spending on durable goods accounted 58% of total spending. Today, it accounts for only 28%. This is because the cost of manufacturing and sale of these goods has dropped while the content has increased. The result is that computers, televisions and sound equipment have fallen in price.
The recovery in manufacturing activity has boosted the production of manufactured goods in the US. The Fifth District Manufacturing Activity Survey reveals that the demand for manufactured products is strong, with production increasing rapidly. However, supply chain problems are slowing down output. The increased production has stressed supply chains. Respondents report that they have experienced supply chain disruptions that impact their ability keep adequate inventories. Backlogs and lead times for vendors have increased.
The trade deficit in manufactured products has more than doubled over the past decade
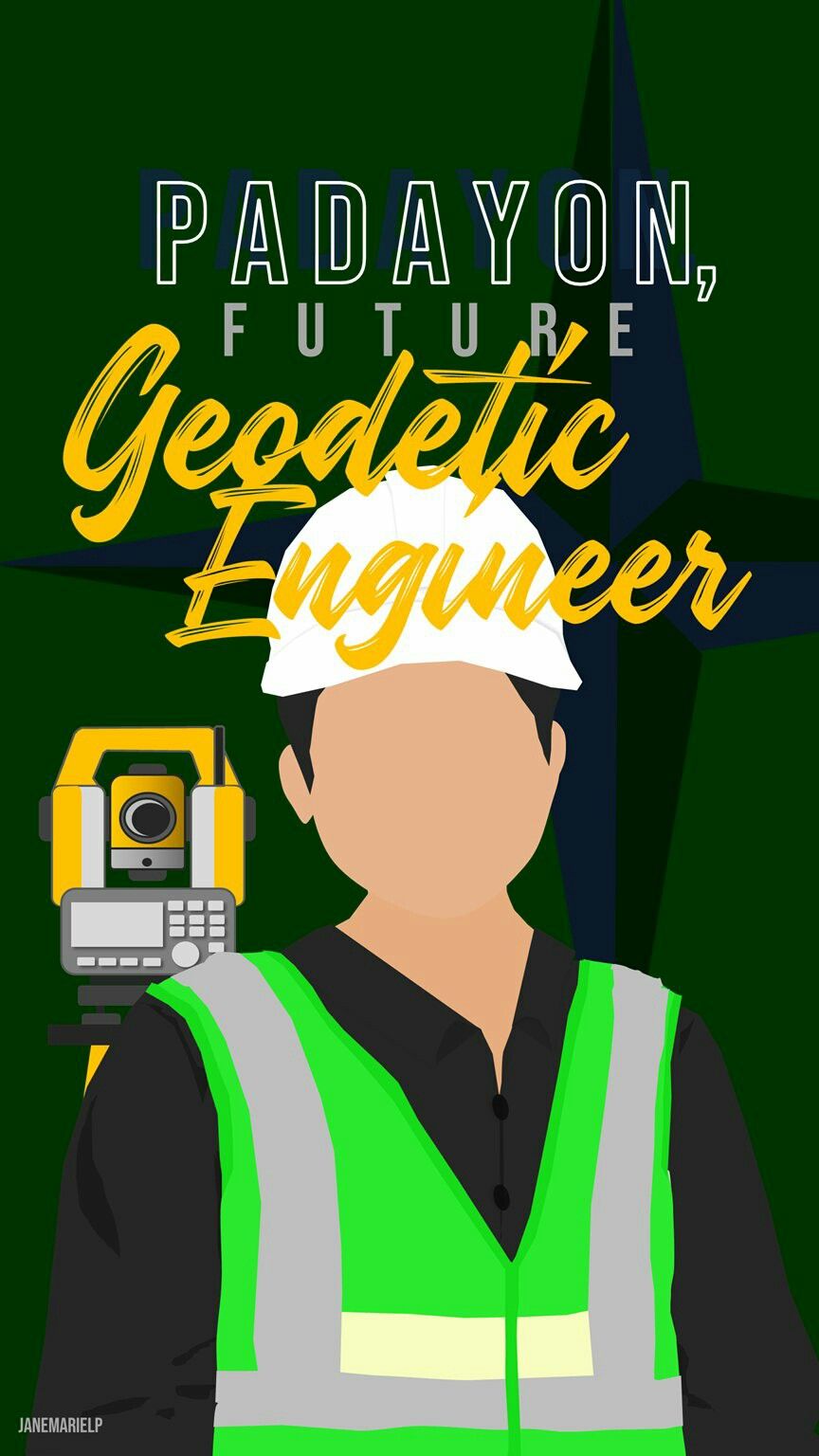
Economists are concerned that the U.S. trade surplus could lead to lower global growth and more instability among its trading partners. Some argue that the high imports of manufactured goods from the United States are not necessarily bad for its economy. This is essential to maintaining global economic stability. High levels of foreign market demand can make it difficult for the U.S. to achieve full employment.
Since 2000, nearly two-thirds of the U.S. manufacturing goods trade deficit has increased. Partially, the US trade deficit in manufactured goods has doubled since 2000. However, the problem is more serious. This imbalance is concentrated in manufacturing where wages have dropped and employment has declined significantly since 1990. As a result, US manufacturing employment has fallen dramatically from 26 percent in 1970 to 8.5 percent in 2016. Some economists attribute the decline to China's increased competition, but most attribute the decline to automation, productivity increases, and demand shifting away from goods to services.
Industry follows a shotgun approach
The US manufacturing sector is well-known for its many advanced manufacturing initiatives. Some countries, however, are taking a more focused approach to bringing the internet into manufacturing. The US, on the other hand, focuses on diverse technologies and combines Internet advertising with traditional mass media. The result is a shotgun approach. Companies focus on many technologies and target a broad client base.
FAQ
What do we need to know about Manufacturing Processes in order to learn more about Logistics?
No. No. But, being familiar with manufacturing processes will give you a better understanding about how logistics works.
What are the differences between these four types?
Manufacturing refers to the transformation of raw materials into useful products by using machines and processes. Manufacturing can include many activities such as designing and building, testing, packaging shipping, selling, servicing, and other related activities.
How can manufacturing avoid production bottlenecks
The key to avoiding bottlenecks in production is to keep all processes running smoothly throughout the entire production cycle, from the time you receive an order until the time when the product ships.
This includes planning for both capacity requirements and quality control measures.
The best way to do this is to use continuous improvement techniques such as Six Sigma.
Six Sigma can be used to improve the quality and decrease waste in all areas of your company.
It emphasizes consistency and eliminating variance in your work.
What are the products and services of logistics?
Logistics refers to the movement of goods from one place to another.
They include all aspects associated with transport including packaging, loading transporting, unloading storage, warehousing inventory management customer service, distribution returns and recycling.
Logisticians ensure the product reaches its destination in the most efficient manner. They assist companies with their supply chain efficiency through information on demand forecasts. Stock levels, production times, and availability.
They coordinate with vendors and suppliers, keep track of shipments, monitor quality standards and perform inventory and order replenishment.
What is the role of a production manager?
Production planners make sure that every aspect of the project is delivered on-time, within budget, and within schedule. They also ensure that the product/service meets the client’s needs.
Why is logistics important in manufacturing
Logistics is an integral part of every business. They are essential to any business's success.
Logistics also play a major role in reducing costs and increasing efficiency.
Is automation important for manufacturing?
Automation is important not only for manufacturers but also for service providers. It allows them to offer services faster and more efficiently. It reduces human errors and improves productivity, which in turn helps them lower their costs.
Statistics
- Many factories witnessed a 30% increase in output due to the shift to electric motors. (en.wikipedia.org)
- According to the United Nations Industrial Development Organization (UNIDO), China is the top manufacturer worldwide by 2019 output, producing 28.7% of the total global manufacturing output, followed by the United States, Japan, Germany, and India.[52][53] (en.wikipedia.org)
- According to a Statista study, U.S. businesses spent $1.63 trillion on logistics in 2019, moving goods from origin to end user through various supply chain network segments. (netsuite.com)
- You can multiply the result by 100 to get the total percent of monthly overhead. (investopedia.com)
- [54][55] These are the top 50 countries by the total value of manufacturing output in US dollars for its noted year according to World Bank.[56] (en.wikipedia.org)
External Links
How To
How to Use the 5S to Increase Productivity In Manufacturing
5S stands to stand for "Sort", “Set In Order", “Standardize", and "Store". The 5S methodology was developed at Toyota Motor Corporation in 1954. This methodology helps companies improve their work environment to increase efficiency.
The idea behind standardizing production processes is to make them repeatable and measurable. Cleaning, sorting and packing are all done daily. Because workers know what they can expect, this helps them perform their jobs more efficiently.
Five steps are required to implement 5S: Sort, Set In Order, Standardize. Separate. Each step involves a different action which leads to increased efficiency. Sorting things makes it easier to find them later. You arrange items by placing them in an order. Then, after you separate your inventory into groups, you store those groups in containers that are easy to access. Finally, when you label your containers, you ensure everything is labeled correctly.
Employees must be able to critically examine their work practices. Employees should understand why they do the tasks they do, and then decide if there are better ways to accomplish them. They will need to develop new skills and techniques in order for the 5S system to be implemented.
The 5S method increases efficiency and morale among employees. They are more motivated to achieve higher efficiency levels as they start to see improvement.