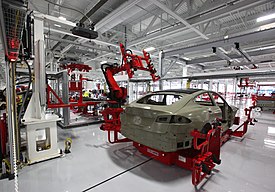
Robotics Technicians are employed by robot manufacturers and robotics suppliers. They are responsible to maintain and repair equipment that is used in the construction and operation of robotic systems. The job requires a degree and hands-on experience. There are many salaries for robotics technicians, depending on experience and education.
Robotics technicians typically earn an associate's degree in a relevant field. This may include electronics, mathematics, or mechanical engineering. A degree in robotics will typically give students a strong background of science, mathematics, programming, and math. The program will prepare a robotics technician to work with a team that includes robotics professionals in order to build, test, and maintain robotic systems.
They are used in nearly every aspect of our daily lives. Robots can be found in many industries. They are used for material handling, transportation, the defense department, and the medical field. A robot can gather information for soldiers, such as landmines, in the military. Mechatronics is an engineering discipline that combines electrical, mechanical, and computer engineering.
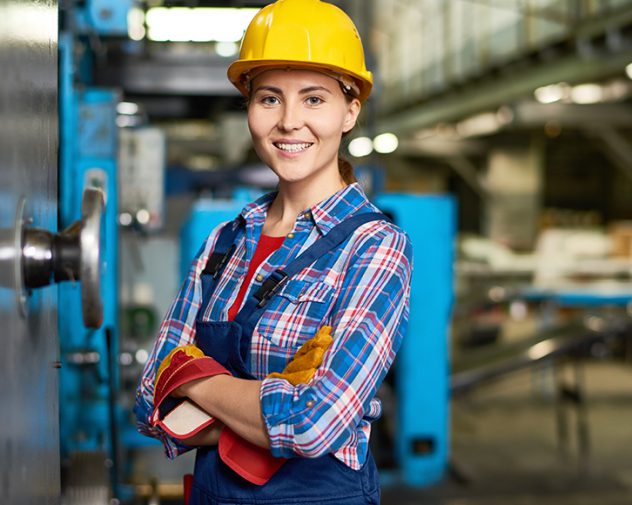
Many colleges and universities offer programs in robotics technician. Robotics technicians are available for hire by companies. A keen interest in problem solving and a strong aptitude for science and math are essential to becoming a successful robotics operator. However, employers will also generally require applicants to have a high school diploma.
Although the robotics technician's salary is not particularly large, the profession does require a considerable degree of education. Robotics technicians typically have a two year associate's degree. It is not uncommon to earn additional training as part of the job, although most of the time the employer will provide some on-the-job training.
Robotics technicians are expected to work around the clock, depending on the industry. Robotics operators are responsible for programming robots in order to complete specific tasks. They must identify the problem and fix it if the robot malfunctions. Operators will also need to work weekends and nights.
Robotics Technicians are typically paid in the range of $44,175 to $84,520. Atlanta, GA is the most desirable city for Robotics Technicians. It has the best quality of life. Robotics Technicians in Atlanta make an average of $1,841 per month.
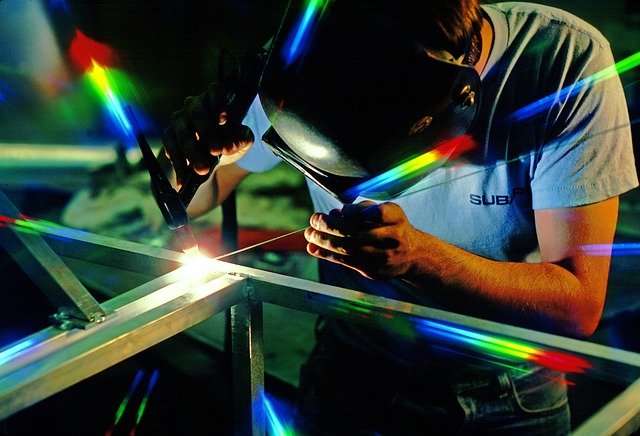
Atlanta residents also have the advantage of a lower state income tax. Georgia's robotics technicians, for example, pay 6% in taxes each year. That is higher than the national average. Atlanta's cost of living is generally lower than other cities making it an attractive place to settle down.
Robotics technicians can be a great fit for people who want a positive impact on the global community. Robotics technicians are highly skilled and can earn great salaries. These individuals can work as maintenance technicians or robotics operators and will be able to share their knowledge and skills with the rest of the world.
FAQ
Why automate your warehouse?
Modern warehousing is becoming more automated. E-commerce has brought increased demand for more efficient and quicker delivery times.
Warehouses should be able adapt quickly to new needs. In order to do this, they need to invest in technology. Automation of warehouses offers many benefits. Here are some reasons why it's worth investing in automation:
-
Increases throughput/productivity
-
Reduces errors
-
Improves accuracy
-
Safety increases
-
Eliminates bottlenecks
-
Allows companies scale more easily
-
This makes workers more productive
-
The warehouse can be viewed from all angles.
-
Enhances customer experience
-
Improves employee satisfaction
-
Reducing downtime and increasing uptime
-
Ensures quality products are delivered on time
-
Removing human error
-
This helps to ensure compliance with regulations
What is meant by manufacturing industries?
Manufacturing Industries are businesses that produce products for sale. These products are sold to consumers. These companies employ many processes to achieve this purpose, such as production and distribution, retailing, management and so on. They produce goods from raw materials by using machines and other machinery. This includes all types of manufactured goods, including food items, clothing, building supplies, furniture, toys, electronics, tools, machinery, vehicles, pharmaceuticals, medical devices, chemicals, and many others.
What are the responsibilities of a manufacturing manager
A manufacturing manager must ensure that all manufacturing processes are efficient and effective. They should also be aware and responsive to any company problems.
They must also be able to communicate with sales and marketing departments.
They should be up to date on the latest trends and be able apply this knowledge to increase productivity and efficiency.
What are the 4 types manufacturing?
Manufacturing is the process of transforming raw materials into useful products using machines and processes. It can involve many activities like designing, manufacturing, testing packaging, shipping, selling and servicing.
Why is logistics important for manufacturing?
Logistics are essential to any business. They enable you to achieve outstanding results by helping manage product flow from raw materials through to finished goods.
Logistics plays a significant role in reducing cost and increasing efficiency.
Statistics
- In the United States, for example, manufacturing makes up 15% of the economic output. (twi-global.com)
- According to a Statista study, U.S. businesses spent $1.63 trillion on logistics in 2019, moving goods from origin to end user through various supply chain network segments. (netsuite.com)
- You can multiply the result by 100 to get the total percent of monthly overhead. (investopedia.com)
- (2:04) MTO is a production technique wherein products are customized according to customer specifications, and production only starts after an order is received. (oracle.com)
- In 2021, an estimated 12.1 million Americans work in the manufacturing sector.6 (investopedia.com)
External Links
How To
How to use 5S to increase Productivity in Manufacturing
5S stands for "Sort", 'Set In Order", 'Standardize', & Separate>. Toyota Motor Corporation created the 5S methodology in 1954. It assists companies in improving their work environments and achieving higher efficiency.
This method aims to standardize production processes so that they are repeatable, measurable and predictable. This means that daily tasks such as cleaning and sorting, storage, packing, labeling, and packaging are possible. Workers can be more productive by knowing what to expect.
Implementing 5S requires five steps. These are Sort, Set In Order, Standardize. Separate. And Store. Each step has a different action and leads to higher efficiency. If you sort items, it makes them easier to find later. You arrange items by placing them in an order. Next, organize your inventory into categories and store them in containers that are easily accessible. Make sure everything is correctly labeled when you label your containers.
This process requires employees to think critically about how they do their job. Employees should understand why they do the tasks they do, and then decide if there are better ways to accomplish them. To implement the 5S system, employees must acquire new skills and techniques.
The 5S Method not only improves efficiency, but it also helps employees to be more productive and happier. They are more motivated to achieve higher efficiency levels as they start to see improvement.