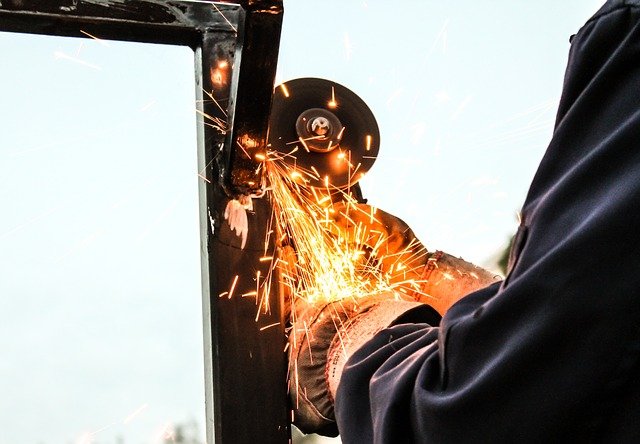
Robotics Suppliers and manufacturers employ robotics technicians. They are responsible for maintaining and repairing equipment used to construct and operate robotic systems. The job requires a degree and hands-on experience. There are many salaries for robotics technicians, depending on experience and education.
A robotics technician typically holds an associate's degree. This could be in electronics, mathematics or mechanical engineering. The degree typically provides a solid background in science, mathematics and computer programming. The program will prepare a robotics technician to work with a team that includes robotics professionals in order to build, test, and maintain robotic systems.
They are used in every aspect our lives. Robots are used in many different industries, such as material handling and transport. A robot can gather information for soldiers, such as landmines, in the military. A discipline in engineering that integrates electrical, mechanical and computer engineering, mechanics is called.
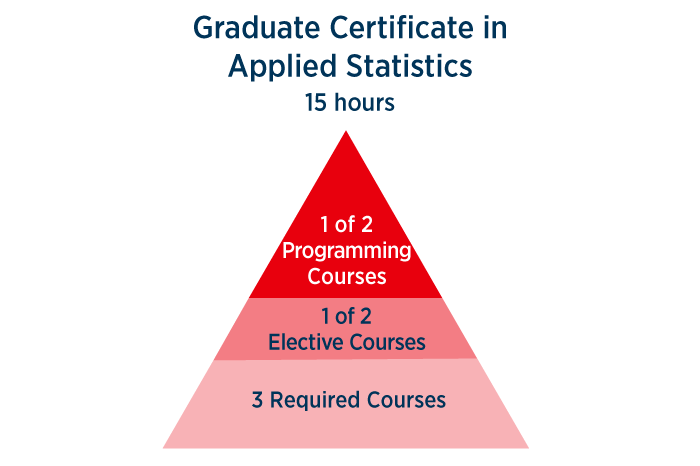
There are many colleges and universities in the United States that offer robotics technician programs. Companies that employ robotics technicians can also offer jobs for students. One must be an enthusiastic problem solver and have a good understanding of math and science in order to become a successful operator. Employers may require applicants to have a high-school diploma.
While the salary for robotics technicians isn't very high, they do require a significant amount of education. Most robotics technicians obtain a two-year associate's degree in robot technology. While it is not unusual to get additional training while working as a robotics technician, the majority of employers provide training on the job.
Robotics technicians are expected to work around the clock, depending on the industry. Robotics technicians are responsible to program robots to do specific tasks. Operators must diagnose the root cause of malfunctioning robots and then repair them. Operators will be required to work nights or weekends.
Robotics technicians typically earn between $44,175 and $84,520. Atlanta, GA has the highest quality of life for Robotics Technicians. This is due to its high quality of living. The average salary for Robotics Technicians is $1,841 per paycheck.
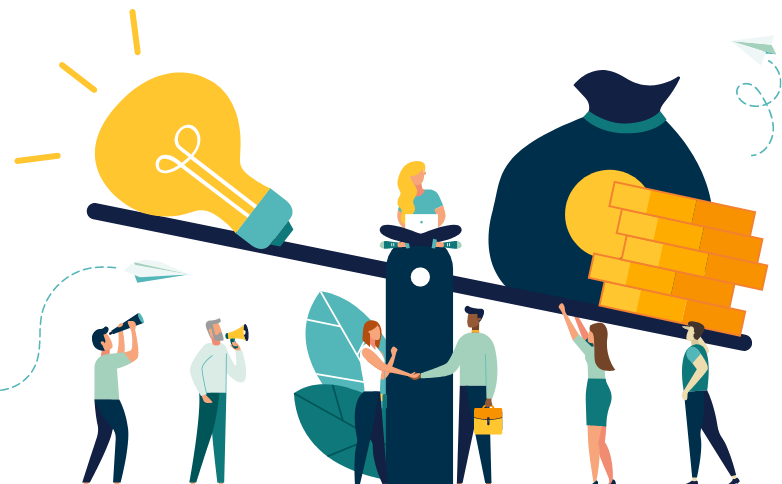
Atlanta's state tax rate is lower for robotics technicians. Georgia robotics technicians are required to pay 6% tax on their salaries. This is higher than what the national average is. Atlanta's cost of living is generally lower than other cities making it an attractive place to settle down.
Robotics technicians make a great choice for those looking to make a real difference in the world. As an expert in the field, a robotics technician can earn excellent salaries. They can be employed as either a maintenance technician, or a robot operator.
FAQ
Is automation necessary in manufacturing?
Automation is essential for both manufacturers and service providers. Automation allows them to deliver services quicker and more efficiently. It helps them to lower costs by reducing human errors, and improving productivity.
Is it possible to automate certain parts of manufacturing
Yes! Automation has been around since ancient times. The wheel was invented by the Egyptians thousands of years ago. To help us build assembly lines, we now have robots.
Actually, robotics can be used in manufacturing for many purposes. These include:
-
Automated assembly line robots
-
Robot welding
-
Robot painting
-
Robotics inspection
-
Robots that make products
Manufacturing could also benefit from automation in other ways. 3D printing is a way to make custom products quickly and without waiting weeks or months for them to be manufactured.
How can manufacturing avoid production bottlenecks
Production bottlenecks can be avoided by ensuring that processes are running smoothly during the entire production process, starting with the receipt of an order and ending when the product ships.
This includes planning for capacity requirements as well as quality control measures.
Continuous improvement techniques like Six Sigma are the best way to achieve this.
Six Sigma is a management method that helps to improve quality and reduce waste.
It is focused on creating consistency and eliminating variation in your work.
How can efficiency in manufacturing be improved?
The first step is to determine the key factors that impact production time. Then we need to find ways to improve these factors. If you don’t know where to begin, consider which factors have the largest impact on production times. Once you have identified them, it is time to identify solutions.
How can we reduce manufacturing overproduction?
In order to reduce excess production, you need to develop better inventory management methods. This would reduce the time spent on unproductive activities like purchasing, storing and maintaining excess stock. This would allow us to use our resources for more productive tasks.
You can do this by adopting a Kanban method. A Kanban board can be used to monitor work progress. A Kanban system allows work items to move through several states before reaching their final destination. Each state is assigned a different priority.
If work is moving from one stage to the other, then the current task can be completed and moved on to the next. A task that is still in the initial stages of a process will be considered complete until it moves on to the next stage.
This helps to keep work moving forward while ensuring that no work is left behind. Managers can monitor the work being done by Kanban boards to see what is happening at any given time. This allows them the ability to adjust their workflow using real-time data.
Lean manufacturing can also be used to reduce inventory levels. Lean manufacturing emphasizes eliminating waste in all phases of production. Waste includes anything that does not add value to the product. There are several types of waste that you might encounter:
-
Overproduction
-
Inventory
-
Packaging not required
-
Material surplus
Manufacturers can increase efficiency and decrease costs by implementing these ideas.
What is the distinction between Production Planning or Scheduling?
Production Planning (PP) refers to the process of determining how much production is needed at any given moment. Forecasting and identifying production capacity are two key elements to this process.
Scheduling involves the assignment of dates and times to tasks in order to complete them within the timeframe.
Statistics
- You can multiply the result by 100 to get the total percent of monthly overhead. (investopedia.com)
- (2:04) MTO is a production technique wherein products are customized according to customer specifications, and production only starts after an order is received. (oracle.com)
- In 2021, an estimated 12.1 million Americans work in the manufacturing sector.6 (investopedia.com)
- In the United States, for example, manufacturing makes up 15% of the economic output. (twi-global.com)
- It's estimated that 10.8% of the U.S. GDP in 2020 was contributed to manufacturing. (investopedia.com)
External Links
How To
How to Use the Just In Time Method in Production
Just-in time (JIT), is a process that reduces costs and increases efficiency in business operations. It's the process of obtaining the right amount and timing of resources when you need them. This means that you only pay the amount you actually use. Frederick Taylor first coined this term while working in the early 1900s as a foreman. After observing how workers were paid overtime for late work, he realized that overtime was a common practice. He decided that workers would be more productive if they had enough time to complete their work before they started to work.
The idea behind JIT is that you should plan ahead and have everything ready so you don't waste money. The entire project should be looked at from start to finish. You need to ensure you have enough resources to tackle any issues that might arise. If you expect problems to arise, you will be able to provide the necessary equipment and personnel to address them. This way you won't be spending more on things that aren’t really needed.
There are many JIT methods.
-
Demand-driven: This type of JIT allows you to order the parts/materials required for your project on a regular basis. This will allow to track how much material has been used up. You'll also be able to estimate how long it will take to produce more.
-
Inventory-based: This allows you to store the materials necessary for your projects in advance. This allows for you to anticipate how much you can sell.
-
Project-driven: This is an approach where you set aside enough funds to cover the cost of your project. You will be able to purchase the right amount of materials if you know what you need.
-
Resource-based JIT : This is probably the most popular type of JIT. Here, you allocate certain resources based on demand. For instance, if you have a lot of orders coming in, you'll assign more people to handle them. If you don't receive many orders, then you'll assign fewer employees to handle the load.
-
Cost-based: This is a similar approach to resource-based but you are not only concerned with how many people you have, but also how much each one costs.
-
Price-based: This is a variant of cost-based. However, instead of focusing on the individual workers' costs, this looks at the total price of the company.
-
Material-based - This is a variant of cost-based. But instead of looking at the total company cost, you focus on how much raw material you spend per year.
-
Time-based: Another variation of resource-based JIT. Instead of focusing only on how much each employee is costing, you should focus on how long it takes to complete your project.
-
Quality-based JIT is another variant of resource-based JIT. Instead of looking at the labor costs and time it takes to make a product, think about its quality.
-
Value-based: This is one of the newest forms of JIT. In this case, you're not concerned with how well the products perform or whether they meet customer expectations. Instead, you are focused on adding value to the marketplace.
-
Stock-based: This inventory-based approach focuses on how many items are being produced at any one time. This method is useful when you want to increase production while decreasing inventory.
-
Just-intime planning (JIT), is a combination JIT/sales chain management. It refers to the process of scheduling the delivery of components as soon as they are ordered. It reduces lead times and improves throughput.