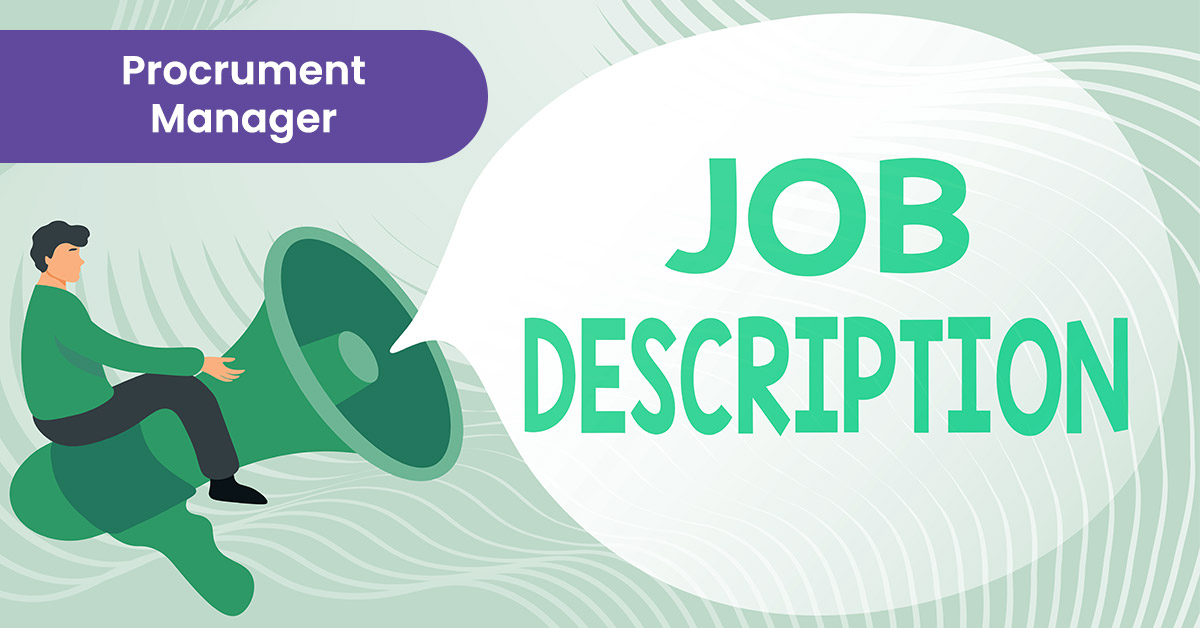
A career as an industrial designer is a rewarding choice for those who love design, or those who are already professionals. Industrial designers work closely with engineers and production professionals to develop product concepts. Industrial designers are responsible for designing products, but also conducting market research and investigating materials. These designers often present their designs and ideas to sales staff and decision-makers. They can work in the industry full time or as freelancers.
Industrial designers create physical prototypes of their designs. Depending on the type of design, these prototypes may be created using different computer-aided design (CAD) and manufacturing tools. The prototypes are used in order to evaluate the function and design of the product. These prototypes serve as a visual representation.
Many industrial designers work together with engineers to create and test prototypes. Prototypes are created using software such as AutoCAD and SolidWorks. They meet with clients to draw their plans. They must possess exceptional artistic and analytical skills.
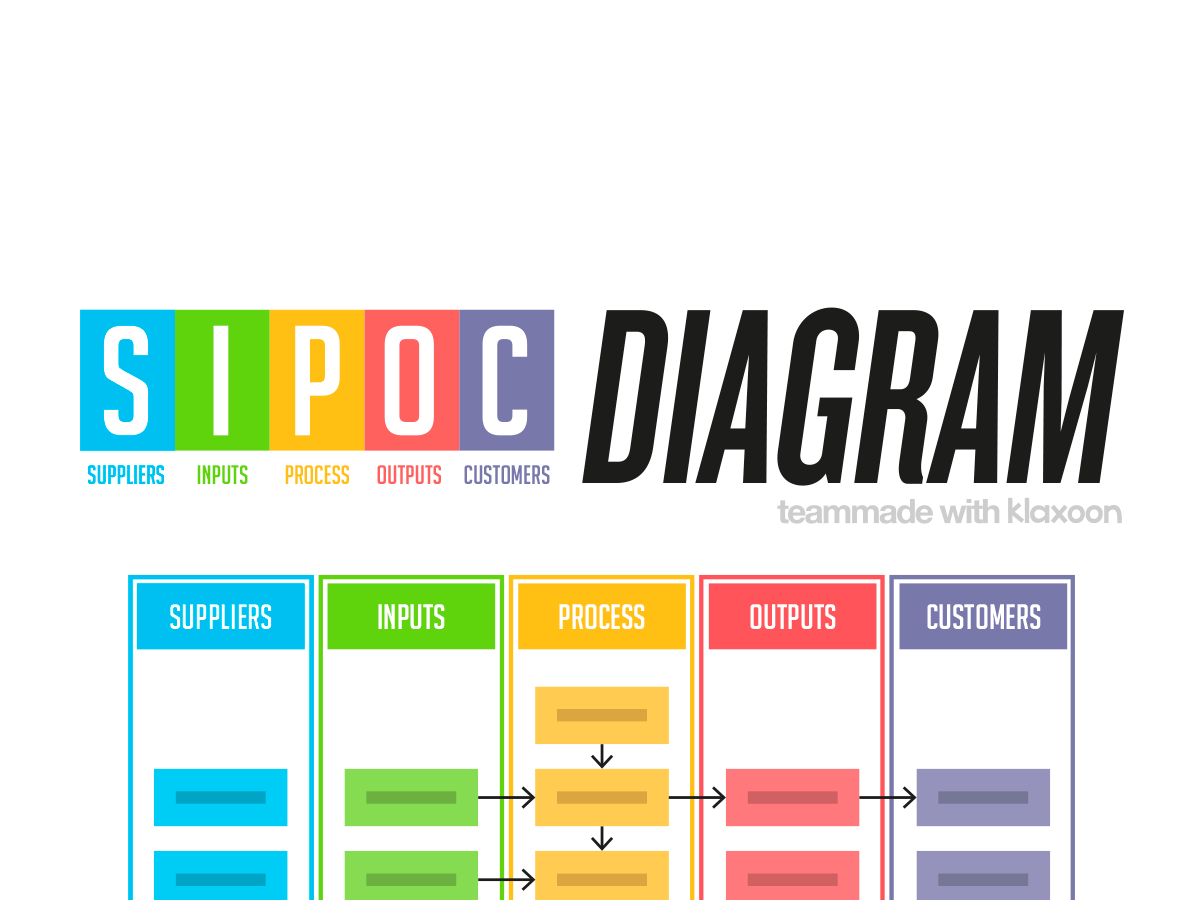
Sometimes industrial designers have to travel to their clients' manufacturing or testing sites. Clients may also require them to meet on weekends and evenings.
Industrial designers can work in an office or freelance. Industrial designers also have the option of working abroad. If you want to work abroad, you will need to pass international exams and communicate in English. You will also need to have a solid education. An industrial designer may work in another country for as long as three years.
For industrial designers, a bachelor's degree is a requirement. Employers often prefer candidates with graphic design skills. An industrial designer might want to enroll in a CAD bootcamp. These classes are typically free and can help to teach you the necessary tools. You can also become a certified professional designer after completing these classes. Industries design firms recognize CAD certification.
Industrial designers must create attractive and functional designs for their products. They design a wide range of products, including medical equipment and consumer electronics. Industrial designers must learn as much as possible about the product they are designing. They also need to be skilled in problem solving and writing. Also, industrial designers work to reduce production costs. They are also highly creative and have a passion for designing products.
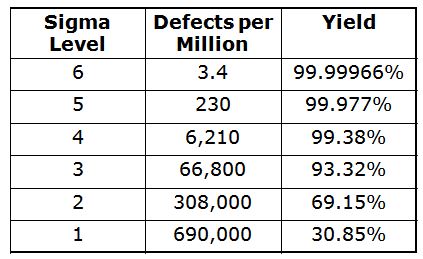
A resume for an industrial designer should reflect their career goals. The resume should also address their work history and the company's specific needs. You should also include an electronic portfolio that shows their previous work. This portfolio can include designs from internships or classes.
Many industrial designers work closely with engineers, production experts, and other professionals to develop prototypes or concepts. They might also be able to work with marketing specialists to promote their products. They frequently present their designs in person to sales personnel and decision makers. They may also travel to their client's testing or manufacturing facilities. They may have to meet with clients or sales representatives on weekends or evenings.
FAQ
What is the importance of automation in manufacturing?
Not only is automation important for manufacturers, but it's also vital for service providers. It enables them to provide services faster and more efficiently. It also helps to reduce costs and improve productivity.
What does manufacturing industry mean?
Manufacturing Industries are companies that manufacture products. Consumers are people who purchase these goods. These companies employ many processes to achieve this purpose, such as production and distribution, retailing, management and so on. They make goods from raw materials with machines and other equipment. This includes all types of manufactured goods, including food items, clothing, building supplies, furniture, toys, electronics, tools, machinery, vehicles, pharmaceuticals, medical devices, chemicals, and many others.
What is production management?
Production Planning is the creation of a plan to cover all aspects, such as scheduling, budgeting. Location, crew, equipment, props and other details. It is important to have everything ready and planned before you start shooting. This document should include information about how to achieve the best results on-set. This includes shooting schedules, locations, cast lists, crew details, and equipment requirements.
The first step is to outline what you want to film. You may have already decided where you would like to shoot, or maybe there are specific locations or sets that you want to use. Once you have determined your scenes and locations, it is time to start figuring out the elements that you will need for each scene. You might decide you need a car, but not sure what make or model. This is where you can look up car models online and narrow down your options by choosing from different makes and models.
After you have chosen the right car, you will be able to begin thinking about accessories. Are you looking for people to sit in the front seats? Or maybe you just need someone to push the car around. Perhaps you would like to change the interior colour from black to white. These questions will help guide you in determining the ideal look and feel for your car. The type of shots that you are looking for is another thing to consider. Will you be filming close-ups or wide angles? Maybe you want to show the engine and the steering wheel. These details will help identify the exact car you wish to film.
Once you have established all the details, you can create a schedule. You can use a schedule to determine when and where you need it to be shot. Every day will have a time for you to arrive at the location, leave when you are leaving and return home when you are done. This way, everyone knows what they need to do and when. If you need to hire extra staff, you can make sure you book them in advance. It is not worth hiring someone who won’t show up because you didn’t tell him.
It is important to calculate the amount of filming days when you are creating your schedule. Some projects may only take a couple of days, while others could last for weeks. You should consider whether you will need more than one shot per week when creating your schedule. Multiplying takes in the same area will result both in increased costs and a longer time. If you are unsure if you need multiple takes, it is better to err on the side of caution and shoot fewer takes rather than risk wasting money.
Another important aspect of production planning is setting budgets. As it will allow you and your team to work within your financial means, setting a realistic budget is crucial. You can always lower the budget if you encounter unexpected problems. It is important to not overestimate how much you will spend. If you underestimate the cost of something, you will have less money left after paying for other items.
Planning production is a tedious process. Once you have a good understanding of how everything works together, planning future projects becomes easy.
What is the difference between Production Planning and Scheduling?
Production Planning (PP), is the process of deciding what production needs to take place at any given time. Forecasting and identifying production capacity are two key elements to this process.
Scheduling is the process of assigning specific dates to tasks so they can be completed within the specified timeframe.
What are my options for learning more about manufacturing
You can learn the most about manufacturing by getting involved in it. However, if that's not possible, you can always read books or watch educational videos.
What skills should a production planner have?
A production planner must be organized, flexible, and able multitask to succeed. You must also be able to communicate effectively with clients and colleagues.
What is the role of a manager in manufacturing?
A manufacturing manager has to ensure that all manufacturing processes work efficiently and effectively. They should be aware of any issues within the company and respond accordingly.
They should also be able communicate with other departments, such as sales or marketing.
They must also keep up-to-date with the latest trends in their field and be able use this information to improve productivity and efficiency.
Statistics
- (2:04) MTO is a production technique wherein products are customized according to customer specifications, and production only starts after an order is received. (oracle.com)
- In the United States, for example, manufacturing makes up 15% of the economic output. (twi-global.com)
- According to the United Nations Industrial Development Organization (UNIDO), China is the top manufacturer worldwide by 2019 output, producing 28.7% of the total global manufacturing output, followed by the United States, Japan, Germany, and India.[52][53] (en.wikipedia.org)
- Many factories witnessed a 30% increase in output due to the shift to electric motors. (en.wikipedia.org)
- [54][55] These are the top 50 countries by the total value of manufacturing output in US dollars for its noted year according to World Bank.[56] (en.wikipedia.org)
External Links
How To
How to use 5S to increase Productivity in Manufacturing
5S stands to stand for "Sort", “Set In Order", “Standardize", and "Store". The 5S methodology was developed at Toyota Motor Corporation in 1954. It assists companies in improving their work environments and achieving higher efficiency.
The basic idea behind this method is to standardize production processes, so they become repeatable, measurable, and predictable. This means that tasks such as cleaning, sorting, storing, packing, and labeling are performed daily. This knowledge allows workers to be more efficient in their work because they are aware of what to expect.
Five steps are required to implement 5S: Sort, Set In Order, Standardize. Separate. Each step requires a different action to increase efficiency. Sorting things makes it easier to find them later. When you set items in an order, you put items together. After you have divided your inventory into groups you can store them in easy-to-reach containers. Make sure everything is correctly labeled when you label your containers.
Employees need to reflect on how they do their jobs. Employees must understand why they do certain tasks and decide if there's another way to accomplish them without relying on the old ways of doing things. To implement the 5S system, employees must acquire new skills and techniques.
The 5S method not only increases efficiency but also boosts morale and teamwork. They are more motivated to achieve higher efficiency levels as they start to see improvement.