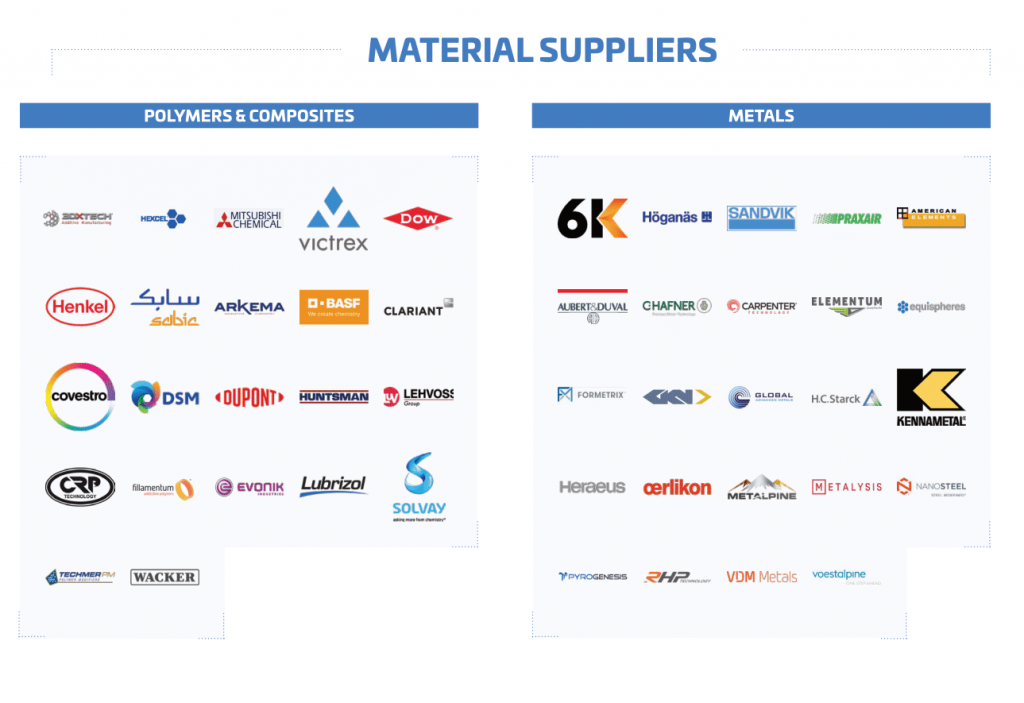
A supply chain manager should have extensive experience in leading manufacturing functions. This means they need to have a bachelor’s degree or higher and should have at most 10 years’ experience. They should also be able to work with other departments within their company. They should be self-motivated with the ability to make important decisions for the company's supply chains. They should also have a good understanding of safety procedures, industry terminology, and terminology.
Supply chain managers manage the logistics process. They are responsible for ensuring that the company's supply network runs smoothly by coordinating with customers, suppliers, as well as other stakeholders. They develop solutions to any problems that arise, and they help to build a productive, functional environment. They also coordinate the company's supply- and distribution strategy.
Responsible for the coordination of phases such as raw material procurement and production, as well distribution, are supply chain managers. They must be able to negotiate prices for materials and equipment, and they must be able to monitor the effectiveness of their supply chain. They are responsible to coordinate and plan transport and storage methods.
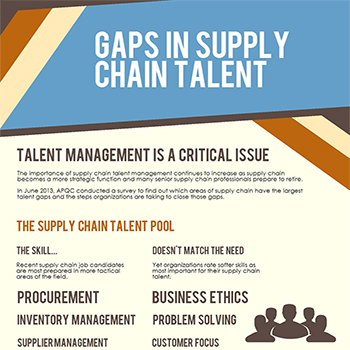
Managers of supply chains are responsible for ensuring that company products are high quality. They also have to optimize the firm's financial and human capital. They are also responsible for identifying opportunities to recycle, reuse, and repurpose materials and products. They must be able to anticipate the needs of all stages of production.
A variety of industries may have supply chain managers such as retail, automotive, fashion, food or food. They must have the ability to work with many departments within their company and to train all employees. They need to be proficient in supply chain management. They should have a strong background in manufacturing and be capable of managing large-scale operations.
Supply chain managers must have specific training in inventory control and supplier management. They must be familiar both with the industry's procedures and policies. They also need to have the ability and skills to manage budgets. They must be adept at organizing systems and be able lead groups. They must also have a thorough understanding of the company's operations and be able to lead their team. They must also have a thorough understanding and appreciation for the company's goals, and they must be able to communicate with suppliers and customers.
Monitoring the environmental performance by their distribution partners is another responsibility of supply chain managers. They may need to investigate the carbon footprint of their storage and transportation providers. They'll also need to monitor the KPIs of their supply chain and be able find solutions to any problems. They will need to look for ways to cut costs, including shipping and delivery.
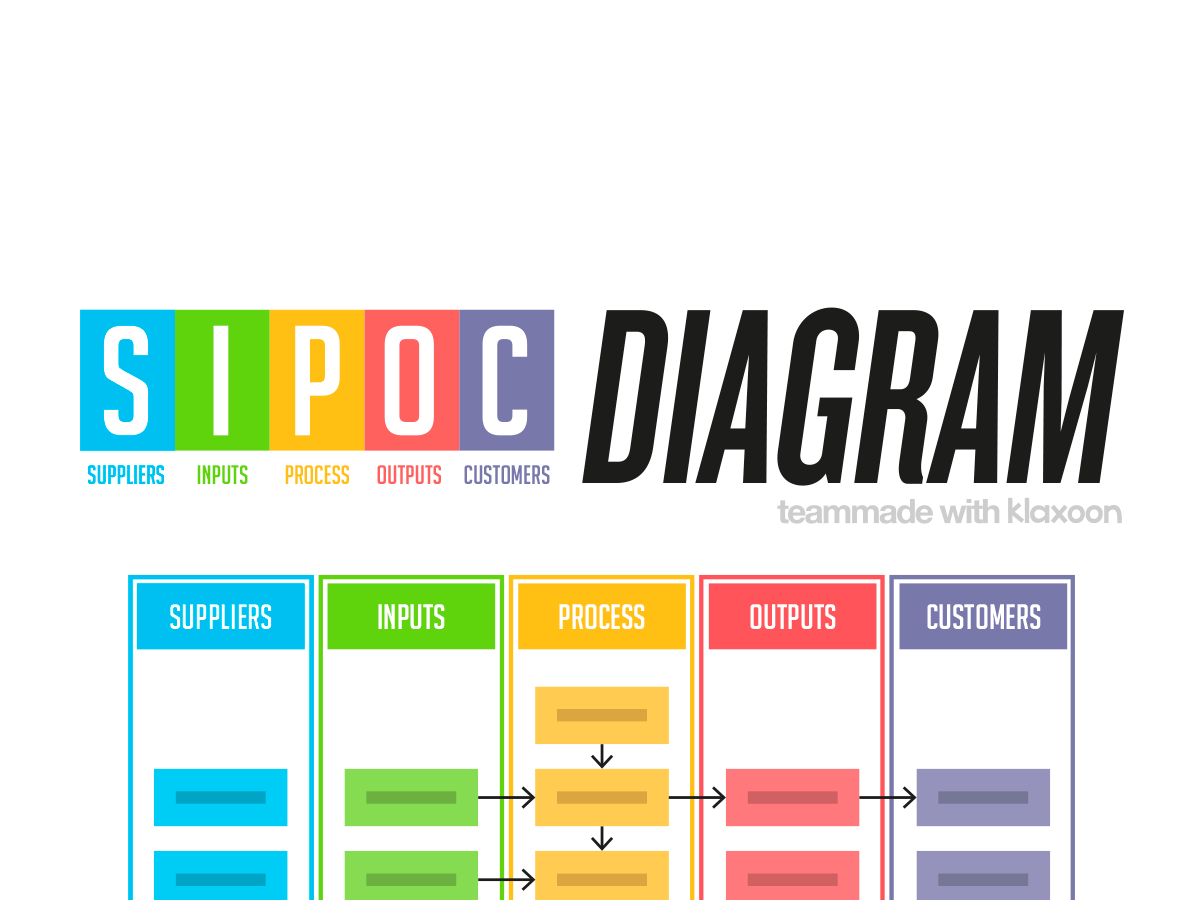
Managers of supply chain work in teams. They coordinate the work and activities of these teams. They are also responsible for training new employees. They must have experience in transportation, purchasing, and manufacturing, and they must have a firm grasp of supply chain management, as well as management principles.
FAQ
What kind of jobs are there in logistics?
Logistics can offer many different jobs. Some examples are:
-
Warehouse workers - They load and unload trucks and pallets.
-
Transportation drivers: They drive trucks and trailers and deliver goods and make pick-ups.
-
Freight handlers - They sort and pack freight in warehouses.
-
Inventory managers: They are responsible for the inventory and management of warehouses.
-
Sales representatives: They sell products to customers.
-
Logistics coordinators are responsible for organizing and planning logistics operations.
-
Purchasing agents – They buy goods or services necessary to run a company.
-
Customer service representatives – They answer emails and phone calls from customers.
-
Shipping clerks - They process shipping orders and issue bills.
-
Order fillers – They fill orders based upon what was ordered and shipped.
-
Quality control inspectors - They check incoming and outgoing products for defects.
-
Others - There are many types of jobs in logistics such as transport supervisors and cargo specialists.
Why is logistics important in manufacturing
Logistics are an essential component of any business. They can help you achieve great success by helping you manage product flow from raw material to finished goods.
Logistics plays a significant role in reducing cost and increasing efficiency.
What skills should a production planner have?
Production planners must be flexible, organized, and able handle multiple tasks. Also, you must be able and willing to communicate with clients and coworkers.
Statistics
- [54][55] These are the top 50 countries by the total value of manufacturing output in US dollars for its noted year according to World Bank.[56] (en.wikipedia.org)
- Many factories witnessed a 30% increase in output due to the shift to electric motors. (en.wikipedia.org)
- In 2021, an estimated 12.1 million Americans work in the manufacturing sector.6 (investopedia.com)
- In the United States, for example, manufacturing makes up 15% of the economic output. (twi-global.com)
- You can multiply the result by 100 to get the total percent of monthly overhead. (investopedia.com)
External Links
How To
Six Sigma in Manufacturing:
Six Sigma is defined by "the application SPC (statistical process control) techniques to achieve continuous improvements." Motorola's Quality Improvement Department in Tokyo, Japan developed Six Sigma in 1986. Six Sigma is a method to improve quality through standardization and elimination of defects. Since there are no perfect products, or services, this approach has been adopted by many companies over the years. The main goal of Six Sigma is to reduce variation from the mean value of production. It is possible to measure the performance of your product against an average and find the percentage of time that it differs from the norm. If you notice a large deviation, then it is time to fix it.
Understanding how your business' variability is a key step towards Six Sigma implementation is the first. Once you have a good understanding of the basics, you can identify potential sources of variation. It is important to identify whether the variations are random or systemic. Random variations are caused by human errors. Systematic variations can be caused by outside factors. These are, for instance, random variations that occur when widgets are made and some fall off the production line. However, if you notice that every time you assemble a widget, it always falls apart at exactly the same place, then that would be a systematic problem.
Once you have identified the problem, you can design solutions. It might mean changing the way you do business or redesigning it entirely. Once you have implemented the changes, it is important to test them again to ensure they work. If they didn't work, then you'll need to go back to the drawing board and come up with another plan.