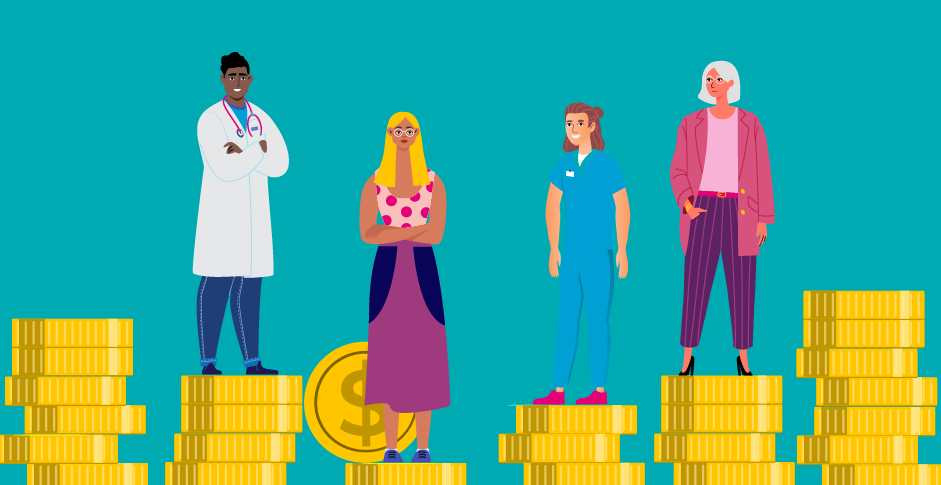
Japanese factories produce high-quality products at low costs. They are the backbone for the country's economy and account for five per cent GDP. They have faced increasing competition, tighter standards, and cost pressures due to the recent recession.
For example, last year, a government white paper found that Japanese firms were unprepared to deal with a parts procurement cutoff. The recession hit the Japanese automobile industry hard. The auto manufacturing industry relies on over 30,000 parts. Any disruption to the supply chain could cause the production to cease. Some parts don't have substitutes.
Japanese manufacturers work closely with suppliers to resolve problems and increase efficiency in order to maintain high quality products. They also encourage workers, salesmen, and quality inspectors to give feedback.
One problem that has been causing concern for Japanese manufacturers is the number of accidents that have occurred on the factory floor. There have been numerous safety scandals in the country's industrial sector. This has led to greater scrutiny of the standard of work in factories.
Another problem that has been affecting the production of Japanese goods is the influx of non-regular employees. The influx of non-regular labor allows companies to lower labor costs but increases the risk of accidents, and de-skills the production floor. Companies are focusing on training regular workers to make them safer and better.
Japan's growing labor shortage is due to the country's declining birthrate. A 25-year high number of Japanese companies are complaining of a lack of labor. If the labor force continues to shrink, Japanese companies will face even greater challenges.
Large numbers of factories are cutting back on costs, despite a shortage in skilled workers. A growing number of so-called "factries" employ fewer than ten people. Many of these small workshops make the best equipment in the country.
Japan's manufacturing sector is being challenged by South Korea and China. As a result, many factories are trying to improve productivity and cut costs. The Japanese government warns that the industry could lose its competitive edge on overseas markets.
Japan is confronted with increased competition from Asia as well as abroad and it is questioning whether its ability to adapt and adjust its processes to meet this demand. And even if it can, the demand for skilled workers is expected to rise.
Japanese factories are a major source of components for global markets. They also supply advanced materials like silicon chips which are used in computers and smart phone. While Chinese factories excel in low-cost assembly operations they still rely on Japan to supply the essential components.
Even as they have worked to improve their productivity and quality, the Japanese have faced increased competition from abroad. They have had to lower their product's value in the domestic marketplace due to the recession. Despite these challenges the Japanese have managed to maintain a high level production standard.
FAQ
What types of jobs can you find in logistics
There are many kinds of jobs available within logistics. Here are some examples:
-
Warehouse workers: They load and unload trucks, pallets, and other cargo.
-
Transportation drivers: They drive trucks and trailers and deliver goods and make pick-ups.
-
Freight handlers – They sort and package freight at warehouses.
-
Inventory managers - These are responsible for overseeing the stock of goods in warehouses.
-
Sales reps are people who sell products to customers.
-
Logistics coordinators are responsible for organizing and planning logistics operations.
-
Purchasing agents - They purchase goods and services needed for company operations.
-
Customer service representatives – They answer emails and phone calls from customers.
-
Shipping clerks: They process shipping requests and issue bills.
-
Order fillers are people who fill orders based only on what was ordered.
-
Quality control inspectors - They check incoming and outgoing products for defects.
-
Others - There are many types of jobs in logistics such as transport supervisors and cargo specialists.
What is the importance of logistics in manufacturing?
Logistics are essential to any business. They enable you to achieve outstanding results by helping manage product flow from raw materials through to finished goods.
Logistics are also important in reducing costs and improving efficiency.
What is the job of a production plan?
Production planners ensure all aspects of the project are delivered within time and budget. They make sure that the product and services meet client expectations.
Statistics
- In 2021, an estimated 12.1 million Americans work in the manufacturing sector.6 (investopedia.com)
- (2:04) MTO is a production technique wherein products are customized according to customer specifications, and production only starts after an order is received. (oracle.com)
- In the United States, for example, manufacturing makes up 15% of the economic output. (twi-global.com)
- According to the United Nations Industrial Development Organization (UNIDO), China is the top manufacturer worldwide by 2019 output, producing 28.7% of the total global manufacturing output, followed by the United States, Japan, Germany, and India.[52][53] (en.wikipedia.org)
- According to a Statista study, U.S. businesses spent $1.63 trillion on logistics in 2019, moving goods from origin to end user through various supply chain network segments. (netsuite.com)
External Links
How To
How to Use Just-In-Time Production
Just-in-time is a way to cut costs and increase efficiency in business processes. It allows you to get the right amount resources at the right time. This means that you only pay for what you actually use. Frederick Taylor, a 1900s foreman, first coined the term. He observed how workers were paid overtime if there were delays in their work. He concluded that if workers were given enough time before they start work, productivity would increase.
JIT is an acronym that means you need to plan ahead so you don’t waste your money. You should also look at the entire project from start to finish and make sure that you have sufficient resources available to deal with any problems that arise during the course of your project. You'll be prepared to handle any potential problems if you know in advance. You won't have to pay more for unnecessary items.
There are many JIT methods.
-
Demand-driven JIT: You order the parts and materials you need for your project every other day. This will enable you to keep track of how much material is left after you use it. This will allow you to calculate how long it will take to make more.
-
Inventory-based: This type allows you to stock the materials needed for your projects ahead of time. This allows one to predict how much they will sell.
-
Project-driven: This is an approach where you set aside enough funds to cover the cost of your project. Knowing how much money you have available will help you purchase the correct amount of materials.
-
Resource-based JIT is the most widespread form. You assign certain resources based off demand. If you have many orders, you will assign more people to manage them. You'll have fewer orders if you have fewer.
-
Cost-based: This approach is very similar to resource-based. However, you don't just care about the number of people you have; you also need to consider how much each person will cost.
-
Price-based: This approach is very similar to the cost-based method except that you don't look at individual workers costs but the total cost of the company.
-
Material-based: This is very similar to cost-based but instead of looking at total costs of the company you are concerned with how many raw materials you use on an average.
-
Time-based JIT is another form of resource-based JIT. Instead of focusing on how much each employee costs, you focus on how long it takes to complete the project.
-
Quality-based JIT: This is another variation of resource based JIT. Instead of looking at the labor costs and time it takes to make a product, think about its quality.
-
Value-based: This is one of the newest forms of JIT. In this case, you're not concerned with how well the products perform or whether they meet customer expectations. Instead, your goal is to add value to the market.
-
Stock-based: This inventory-based approach focuses on how many items are being produced at any one time. This method is useful when you want to increase production while decreasing inventory.
-
Just-in time (JIT), planning: This is a combination JIT/supply chain management. It's the process of scheduling delivery of components immediately after they are ordered. It's important as it reduces leadtimes and increases throughput.