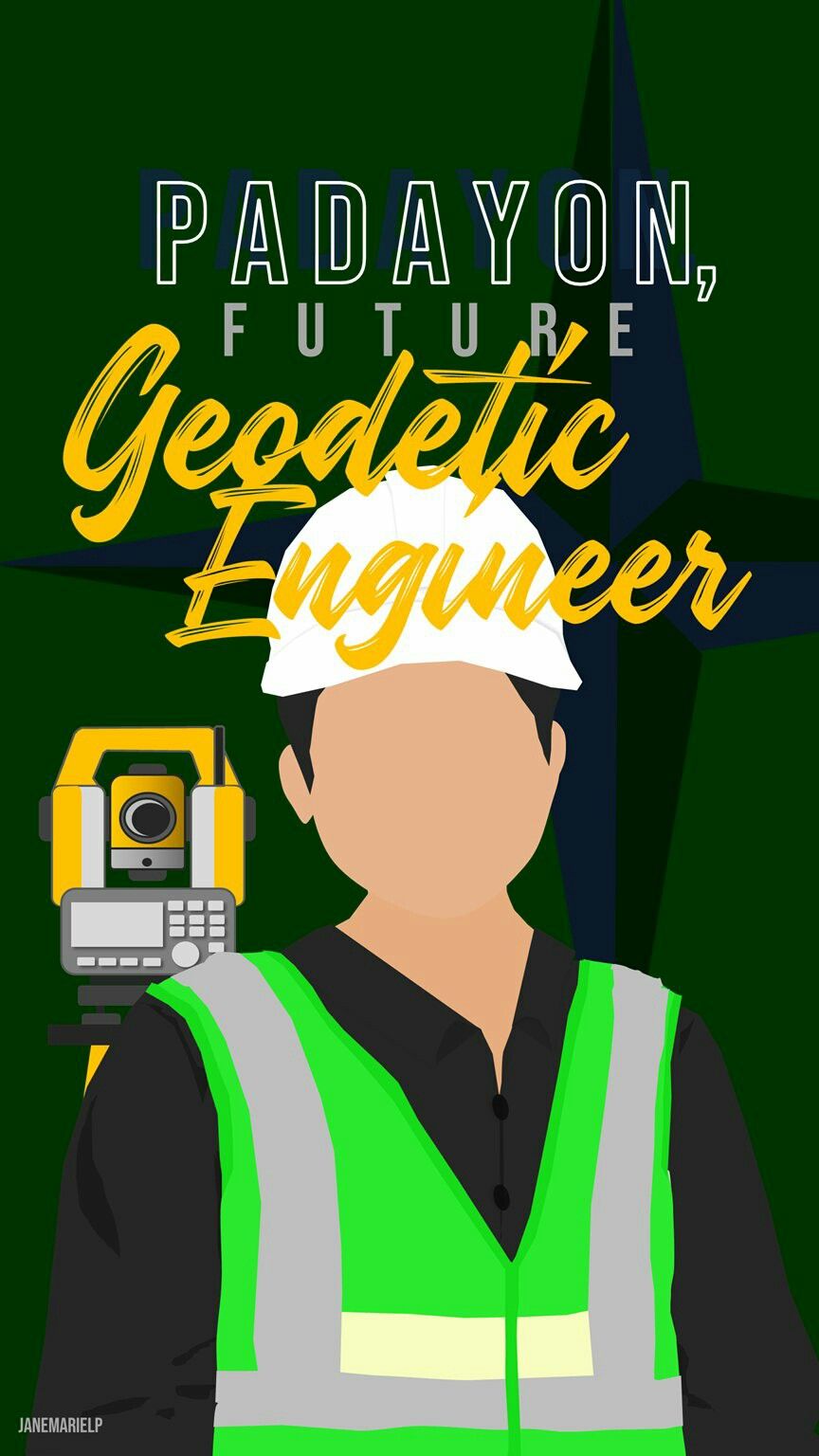
If you are interested in a biochemical salary, you're in the right place. This article will cover biochemical salary in BOTHELL WA as well as San Mateo CA. Explore the various biochemical salaries options to get started in your career. Learn more about the job descriptions and salary requirements at Worthington Biochemical and Youtell Biochemical. Both companies have BOTHELL, WA headquarters and offer competitive benefits.
Youtell Biochemical's hourly salary is $29
Youtell Biochemical offers an average salary of $99854. Salary ranges from $88,159 - $114,509. However, individual salaries can vary wildly depending on the position, department, education, and skills required. Here are some examples for the types and salaries at Youtell Biochemical. Remember that education and experience are important factors in determining the range of salaries.
Youtell Biochemical's headquarters is located in BOTHELL WA
Youtell Biochemical is a chemical firm based in BOTHELL WA that specializes in enzyme products. They have a state -of-the art biotechnology research center at Bothell, and two downstream process and fermentation plants in China. These companies produce enzyme products using patent technologies. Youtell Biochemical's main campus is located in BOTHELL WA and produces more than 80,000 tons of enzymes per year.
Worthington Biochemical has its headquarters in San Mateo, CA.
Worthington Biochemical started in 1947. Charles Worthington was a Rockefeller Institute research assistant who had prepared crystalline enzymes for biochemical research. He saw that the biochemical community was growing and needed high-purity enzymes. Researchers would have to spend a lot time purifying them. Worthington created its own company, Freehold, New Jersey in 1947, to provide these enzymes.
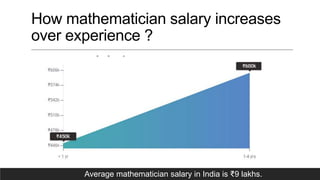
Worthington purchased the New Jersey-based biotech company, Clinical Division of Cooper in 1985. Worthington was able to expand its operations while still focusing on the lucrative clinical market. The company failed to venture into the areas of molecular and immunology. Instead, the company increased its ability to develop diagnostic kits while focusing less on enzyme production.
FAQ
What is the difference between a production planner and a project manager?
The difference between a product planner and project manager is that a planer is typically the one who organizes and plans the entire project. A production planner, however, is mostly involved in the planning stages.
What skills is required for a production planner?
Being a production planner is not easy. You need to be organized and flexible. Effective communication with clients and colleagues is essential.
What are the 7 Rs of logistics.
The 7R's of Logistics is an acronym for the seven basic principles of logistics management. It was developed by the International Association of Business Logisticians (IABL) and published in 2004 as part of its "Seven Principles of Logistics Management" series.
The acronym consists of the following letters:
-
Responsible - to ensure that all actions are within the legal requirements and are not detrimental to others.
-
Reliable - Have confidence in your ability to fulfill all of your commitments.
-
Use resources effectively and sparingly.
-
Realistic - consider all aspects of operations, including cost-effectiveness and environmental impact.
-
Respectful - show respect and treat others fairly and fairly
-
Resourceful - look for opportunities to save money and increase productivity.
-
Recognizable: Provide customers with value-added service
What is the job of a logistics manger?
A logistics manager ensures that all goods are delivered on time and without damage. This is done using his/her knowledge of the company's products. He/she must also ensure sufficient stock to meet the demand.
Why automate your warehouse
Modern warehouses are increasingly dependent on automation. E-commerce has increased the demand for quicker delivery times and more efficient processes.
Warehouses need to adapt quickly to meet changing needs. To do so, they must invest heavily in technology. The benefits of automating warehouses are numerous. Here are some of the reasons automation is worth your investment:
-
Increases throughput/productivity
-
Reduces errors
-
Improves accuracy
-
Boosts safety
-
Eliminates bottlenecks
-
Allows companies scale more easily
-
This makes workers more productive
-
The warehouse can be viewed from all angles.
-
Enhances customer experience
-
Improves employee satisfaction
-
Reducing downtime and increasing uptime
-
Ensures quality products are delivered on time
-
Human error can be eliminated
-
This helps to ensure compliance with regulations
Statistics
- According to a Statista study, U.S. businesses spent $1.63 trillion on logistics in 2019, moving goods from origin to end user through various supply chain network segments. (netsuite.com)
- (2:04) MTO is a production technique wherein products are customized according to customer specifications, and production only starts after an order is received. (oracle.com)
- In 2021, an estimated 12.1 million Americans work in the manufacturing sector.6 (investopedia.com)
- According to the United Nations Industrial Development Organization (UNIDO), China is the top manufacturer worldwide by 2019 output, producing 28.7% of the total global manufacturing output, followed by the United States, Japan, Germany, and India.[52][53] (en.wikipedia.org)
- In the United States, for example, manufacturing makes up 15% of the economic output. (twi-global.com)
External Links
How To
Six Sigma in Manufacturing
Six Sigma is defined as "the application of statistical process control (SPC) techniques to achieve continuous improvement." Motorola's Quality Improvement Department in Tokyo, Japan developed Six Sigma in 1986. Six Sigma is a method to improve quality through standardization and elimination of defects. In recent years, many companies have adopted this method because they believe there is no such thing as perfect products or services. Six Sigma's main objective is to reduce variations from the production average. You can calculate the percentage of deviation from the norm by taking a sample of your product and comparing it to the average. If the deviation is excessive, it's likely that something needs to be fixed.
Understanding how your business' variability is a key step towards Six Sigma implementation is the first. Once you have a good understanding of the basics, you can identify potential sources of variation. Also, you will need to identify the sources of variation. Random variations occur when people make mistakes; systematic ones are caused by factors outside the process itself. Random variations would include, for example, the failure of some widgets to fall from the assembly line. It would be considered a systematic problem if every widget that you build falls apart at the same location each time.
Once you have identified the problem, you can design solutions. This could mean changing your approach or redesigning the entire process. Once you have implemented the changes, it is important to test them again to ensure they work. If they didn't work, then you'll need to go back to the drawing board and come up with another plan.